When it comes to creating the perfect night’s sleep, the quality of your bedding plays a crucial role. But have you ever wondered how your favorite comforter, duvet, or sheet set is made? The bedding manufacturing process combines traditional craftsmanship with advanced technology to deliver products that are soft, durable, and comfortable. In this blog, we’ll explore the key steps and technologies involved in modern bedding manufacturing.
1. Raw Material Selection
The journey of premium bedding begins with the careful selection of raw materials. The most common fabrics used in bedding include:
- Cotton – Known for its softness, breathability, and durability.
- Polyester & Microfiber – Popular for their affordability, wrinkle resistance, and easy care.
- Natural Down & Feather – Used for luxury duvets and pillows, offering superior warmth and comfort.
High-quality manufacturers source only the best fibers, often choosing long-staple cotton or high-grade microfiber to ensure a soft and long-lasting product.
2. Spinning and Weaving
Once the raw materials are selected, the fibers undergo spinning to create yarns. Modern spinning machines ensure consistency and strength in the yarn. Next, weaving machines—often using advanced looms—turn these yarns into fabric. Popular weaves include percale, sateen, and twill, each offering unique textures and benefits.
Key Technologies:
- Automated spinning and weaving machines
- Computerized quality control systems
3. Dyeing and Finishing
After weaving, the fabric is dyed to achieve the desired color and pattern. Advanced dyeing technologies ensure even, vibrant, and long-lasting colors while minimizing environmental impact. The finishing process can include treatments for softness, wrinkle resistance, and stain protection.
Key Technologies:
- Eco-friendly dyeing processes
- Softening and anti-pilling treatments
4. Cutting and Sewing
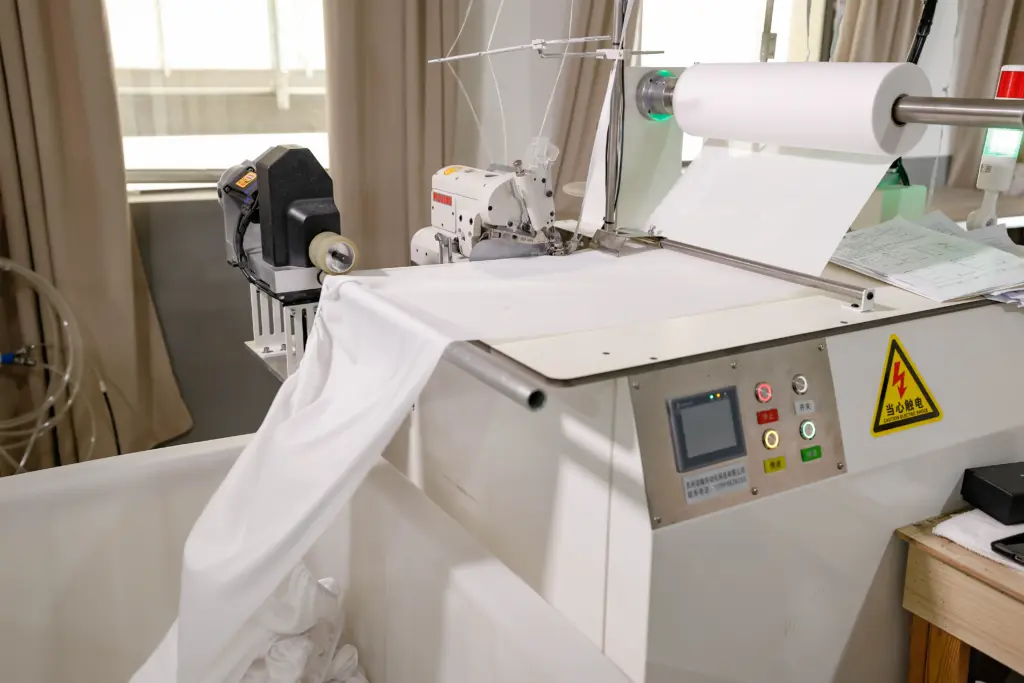
The finished fabric is then cut into precise shapes and sizes for sheets, pillowcases, comforters, and duvets. Computerized cutting machines maximize efficiency and reduce waste. Skilled workers or automated sewing machines assemble the pieces, adding features like piping, zippers, or button closures for both function and style.
Key Technologies:
- CNC fabric cutting machines
- Automated sewing systems
5. Filling and Quilting
For comforters, duvets, and pillows, the filling process is critical. Natural down, feather, or synthetic fibers are evenly distributed inside the fabric shell. Quilting machines stitch the layers together in patterns such as squares, diamonds, or channels, ensuring the filling stays in place and the product maintains its shape.
Key Technologies:
- Precision filling machines
- Computerized quilting machines
6. Quality Control and Packaging
Before leaving the factory, every bedding product undergoes rigorous quality checks for stitching, sizing, and overall appearance. Some manufacturers use advanced inspection systems to detect defects and ensure consistency. Finally, the products are packaged—often in eco-friendly materials—and prepared for shipping worldwide.
Key Technologies:
- Automated inspection systems
- Sustainable packaging solutions
Embracing Innovation in Bedding Manufacturing
Today’s bedding manufacturers continue to innovate by adopting smart technologies such as AI-driven quality control, automated logistics, and sustainable production methods. These advancements not only improve product quality but also reduce environmental impact, ensuring a better sleep experience for customers and a healthier planet.
Conclusion
The bedding manufacturing process is a fascinating blend of art and science. From selecting the finest fibers to using cutting-edge machinery, every step is designed to deliver comfort, durability, and style. As technology continues to evolve, expect even greater innovations in the world of bedding—making your sleep more restful than ever.
Looking for premium bedding products manufactured with the latest technology? Contact Yintex for wholesale and OEM solutions tailored to your needs!
Leave a Reply